Lens manufacturing technology lies at the heart of the eyewear industry, ensuring practitioners deliver optimal vision solutions to their customers. For eyewear retailers and optometrists, understanding the fundamentals—ranging from materials and production processes to coating techniques—can translate into better product quality, improved client satisfaction, and an enhanced reputation. In this blog post, we’ll explore how lenses are made, detail the core components of modern lens manufacturing, and examine proven processes that stand the test of time. We’ll also discuss important quality control measures and highlight practical ways you can implement these techniques. Read on to discover how these battle-tested technologies continue to shape the eyewear industry today.
Table of Contents
- Introduction to Lens Manufacturing Technology
- Key Materials for Modern Eyeglass Lenses
- Core Manufacturing Processes
- Coating Processes and Protective Treatments
- Quality Control and Inspection
- Sustainability in Lens Manufacturing
- Practical Usage and Implementation
- Conclusion
1. Introduction to Lens Manufacturing Technology
Lens manufacturing technology has evolved substantially over the decades, but at its core, it remains a meticulously precise process. Lens manufacturers rely on advanced equipment and skilled labor to transform raw materials into functional, high-quality eyeglass lenses. Because patients’ vision needs vary—due to factors like prescription strength, lens thickness requirements, and desired finishes—the process must remain flexible while maintaining strict quality standards.
For eyewear retailers and optometrists, having a working knowledge of how lenses are designed, molded, surfaced, and coated provides valuable insights. By understanding the manufacturing intricacies, you can offer better recommendations to your customers, anticipate their concerns, and ensure the products you supply align with the highest quality benchmarks in the eyewear industry.
2. Key Materials for Modern Eyeglass Lenses
CR-39 (Plastic)
- Overview: CR-39 was once the gold standard for plastic eyeglass lenses. Its name stems from the Columbia Resin project, and it remains popular due to its excellent optical clarity and lightweight feel.
- Pros: Affordable, easy to work with, and highly compatible with most coating processes.
- Cons: Lower impact resistance compared to other plastics like polycarbonate.
Polycarbonate
- Overview: Known for its durability and impact resistance, polycarbonate lenses are a top choice for children’s eyewear and sports glasses.
- Pros: High impact resistance, natural UV protection, relatively lightweight.
- Cons: Can be more prone to scratching if not properly coated with scratch-resistant coatings.
High-Index Plastics
- Overview: High-index lenses are designed for higher prescriptions, minimizing thickness without compromising optical precision.
- Pros: Thinner and lighter, especially beneficial for strong prescriptions.
- Cons: Typically more expensive, with higher manufacturing costs.
Trivex
- Overview: A relatively newer material (compared to CR-39), Trivex combines many benefits: excellent clarity, high impact resistance, and an ultra-lightweight feel.
- Pros: Offers a balance of clarity and durability, naturally blocks UV rays.
- Cons: More expensive than standard plastic, can be harder to source depending on your supplier.
By choosing the most suitable lens material, you help ensure your clients receive both optimal vision and desirable aesthetics. For additional guidance on selecting the best lens material for specific needs, consider reading our comprehensive materials guide here.
3. Core Manufacturing Processes
3.1 Molding and Surfacing
Once the raw material is chosen, manufacturers either cast mold or grind and surface the lens to achieve the desired prescription.
- Cast Molding: Used primarily for simpler prescriptions or stock lenses. Liquid monomer (if plastic) is poured into molds, exposed to heat and/or UV light, and cured into solid lenses.
- Surfacing: For custom prescriptions, lens blanks are ground using computerized machines. The front surface might already have a specific base curve, while the back surface is carefully ground to match the patient’s prescription.
3.2 Edging and Fitting
After surfacing, the lenses are edged to fit into frames. This process involves:
- Tracing the frame shape.
- Edging the lens to match the traced shape.
- Finishing the edges or applying specialized finishes based on frame requirements (rimless, half-rim, etc.).
Accurate edging ensures a snug fit within the eyewear frame, preventing lens movement and preserving visual alignment.
3.3 Polishing
Polishing is crucial to remove scratches or imperfections introduced during the surfacing process. Any subtle misalignment can lead to distortions in optical technology, so thorough polishing and cleaning are integral to maintaining lens quality.
Alt text for an example image: “Alt text: A lens edging machine precisely shaping an eyeglass lens.”
4. Coating Processes and Protective Treatments
4.1 Anti-Reflective (AR) Coatings
Anti-reflective coatings reduce glare and improve visual clarity, especially for clients who frequently use digital devices or drive at night.
- Application Method: Vacuum deposition, which bonds multiple layers of metal oxides onto the lens surface.
- Benefits: Reduced reflections, enhanced cosmetic appearance, improved visual comfort.
4.2 Scratch-Resistant Coatings
While most lenses naturally include a scratch-resistant layer, an additional coating can fortify the surface. In the lens manufacturing technology process, a hard coat is generally applied, which preserves clarity by preventing superficial scrapes.
4.3 UV Protection
Modern lens materials like polycarbonate and Trivex inherently offer UV protection. However, for materials that lack full coverage, a UV-blocking coat may be applied to ensure that the finished product filters out harmful UVA and UVB rays.
4.4 Photochromic Treatments
Photochromic lenses adapt their tint based on ambient light conditions. Although not a standalone lens manufacturing step, these treatments are integrated into the lens’ molecular structure during production or coated on top in certain specialized processes.
For more insights into maximizing the lifespan of coatings, check out our tips on coating care and maintenance.
5. Quality Control and Inspection
Quality control in lens manufacturing comprises rigorous checks and balances. Common steps include:
- Visual Inspection: Trained professionals look for surface defects, scratches, or any visual distortions.
- Lensometry: Ensures the correct prescription strength and verifies optical precision.
- Thickness Measurement: Confirms uniform thickness and compliance with safety standards.
- Coating Adhesion Tests: Verifies that AR or scratch-resistant layers are properly bonded.
By committing to these inspection measures, manufacturers maintain consistency and uphold reliability, which is crucial for eyewear retailers and optometrists looking to build trust with clients.
6. Sustainability in Lens Manufacturing
Today’s conscientious consumers expect businesses—whether large-scale manufacturers or independent optical practices—to adopt environmentally friendly practices. While lens manufacturing has traditionally relied on energy-intensive processes, many companies are making strides by:
- Minimizing Waste: Reusing or recycling lens blanks and investing in more efficient material usage.
- Using Eco-Friendly Coatings: Implementing solvent-free, water-based coatings to reduce environmental impact.
- Reducing Water Consumption: Incorporating closed-loop water filtration in polishing and edging.
- Adopting Energy-Efficient Equipment: Upgrading to machines with lower energy requirements can lessen the facility’s overall carbon footprint.
7. Practical Usage and Implementation
7.1 Communicating with Suppliers
For eyewear retailers and optometrists, partnering with reputable manufacturers ensures your supply chain remains reliable and transparent. Ask about:
- Their manufacturing techniques
- Coating options
- Quality control practices
- Sustainability initiatives
When you align your practice with a supplier who prioritizes these aspects, you can offer consistent quality to your clients.
7.2 Selecting the Right Coating Packages
Recommend lens and coating packages tailored to each patient’s lifestyle. For example:
- Scratch-Resistant + AR Coating: Ideal for professionals using computers extensively.
- UV Protection + Photochromic: Suited to those spending significant time outdoors.
Matching practical features with an individual’s specific needs increases wearer satisfaction and fosters long-term brand loyalty.
7.3 Educating Your Clients
Empower your customers with knowledge about lens manufacturing technology. Simple explanations of how lenses are made and coated can be incredibly persuasive. Offer pamphlets, infographics, or a quick video demonstration in-store. Doing so may justify higher price points if your practice invests in better coatings or more advanced manufacturing options.
7.4 Internal Training
Keep your team up to date on lens manufacturing fundamentals. Regularly share insights on:
- Emerging, battle-tested processes
- Material developments (like new high-index options)
- Coating innovations that remain proven over time
The more your team knows, the better they can educate clients.
8. Conclusion
Lens manufacturing technology is an intricate balance of materials science, mechanical precision, and coating expertise. For eyewear retailers and optometrists, grasping these core concepts helps in delivering premium eyewear solutions that meet the unique demands of each customer. Whether you’re exploring traditional plastic lenses like CR-39, robust polycarbonate, or high-index materials, adhering to proven industry methods ensures longevity and quality.
From casting and surfacing to coating processes and quality control, every stage matters. By partnering with manufacturers that prioritize both performance and sustainability, you position your practice at the forefront of trust and reliability. Emphasizing proper lens care and recommending the right combination of coatings further bolsters wearer satisfaction.
Take the next step by examining your current supplier relationships, reviewing your in-store educational materials, and reinforcing your team’s knowledge. By integrating these industry best practices, you not only elevate your product offerings but also strengthen your standing in a competitive marketplace—proving you’re fully committed to providing the best in optical technology.
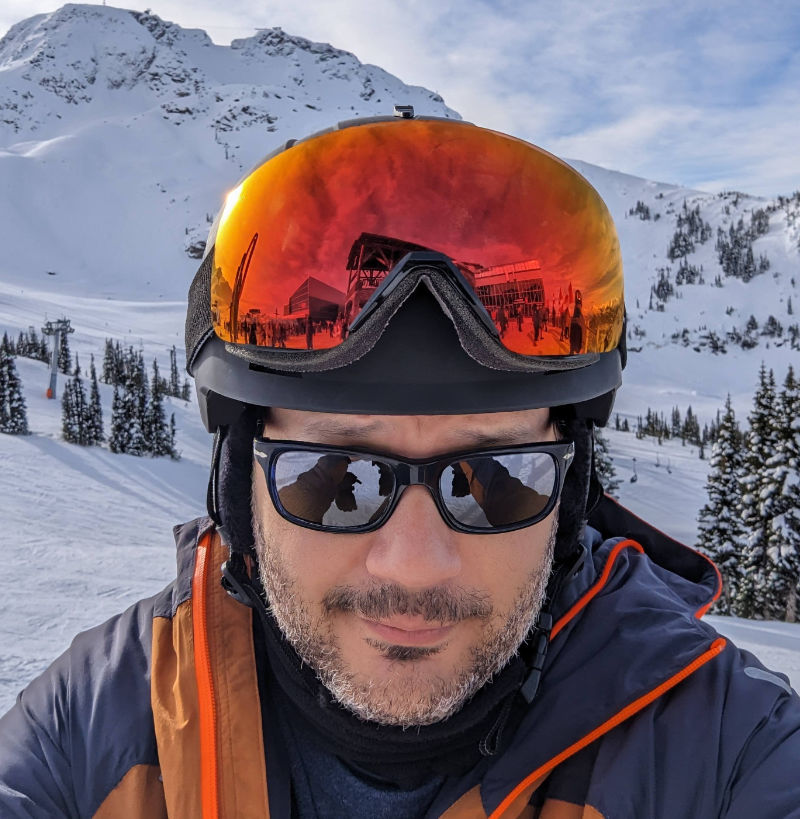
I am a seasoned software engineer with over two decades of experience and a deep-rooted background in the optical industry, thanks to a family business. Driven by a passion for developing impactful software solutions, I pride myself on being a dedicated problem solver who strives to transform challenges into opportunities for innovation.